Fiber optic splice enclosures and quality control
Splice Enclosure Construction
A sailor’s worst nightmare is the failure of a spliced line under strain. Similarly, a NOC’s (network operation center), worst nightmare is a cable cut on an active network. If this happens customers are down, data does not flow, and revenue is lost. Reliability and speed are key selling points for companies providing data transmission services. Their reputations are built on it. Splicing and splice enclosures are critical components in any optical network’s chain of components. This case study will focus on quality control as it applies to the repair of cables and the organization of fibers in splice enclosures.
OVERVIEW
Much has been written on quality control as it applies to the process of fiber splicing. Cleanliness, proper tools, techniques, testing, are all part of the process of splicing a fiber optic cable. That topic will not be discussed here. But the organization of the tubes and fibers inside the enclosure, and the proper sealing of the splice enclosure will be discussed. This is a complicated topic because the organization of a splice enclosure can be affected by multiple factors from the design of the enclosure, to the repair of it in the field.
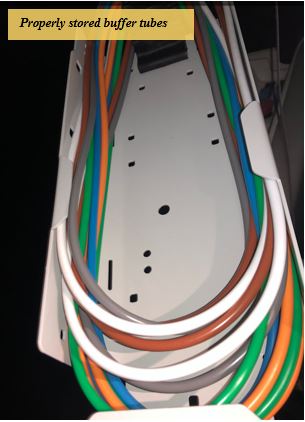
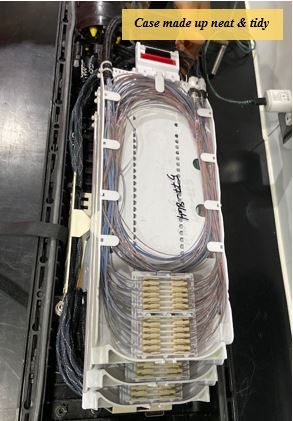
Splice enclosures are rugged and waterproof. They can be found in manholes or hanging off messenger wires in between power poles. They are in service for years and sometimes decades. The enclosure may have to be opened several times per year, or, in urban areas several times per month. They come in various designs and sizes; they have different numbers of weatherproof ports that are designed for specific types of cables.
If the fiber inside the enclosure is spliced and organized properly, and it is installed properly, with sufficient slack and the right strain relief, then the NOC’s should have few concerns when splicing is called for and the enclosure has to be moved from its normal position to the inside of a climate controlled, splice trailer and opened for splicing.
Electric Conduit Construction has internal quality controls in place to assure that splice enclosures are organized and installed properly. We assure that this happens by establishing standards, training our employees, inspecting their work. Every enclosure is photographed before and after and detailed logs are maintained with specifics on how the work was performed and which fibers were spliced. It is part of our company’s procedures and our quality control program.
SPLICE ENCLOSURES & POOR WORKMANSHIP
Unfortunately splice enclosures can become the weak link in the network. Some of the reasons include:
- System modification design may call for enclosures incompatible with existing cables
- Existing enclosure cannot accommodate more cables
- Poor workmanship makes fibers inaccessible
- Poor workmanship places micro-bends in fibers
- Improper installation places excess strain on fibers
- New ports cut into enclosure may compromise integrity of enclosure
- Improper assembly may compromise enclosure integrity
ENCLOSURE FAILURE
Most of the problems with enclosures result from poor workmanship, but it is not the only reason an enclosure fails. Even with new construction or system modifications it is possible to end up with enclosure and cable incompatibility. The problem is compounded when the contractor does not work with the customer to explain the situation and change it. Or sometimes the contractor will just “make it work”, this may work for the short term the installation will not reach its design life. Contractors should be thinking about the quality and resiliency of the customer’s assets. But if the splicing technician is not trained properly and not thinking ahead the work will be rushed to completion leaving the possibility for problems in the future.
Poor workmanship can lead to failure of individual or multiple fiber strands. Failure can occur when insufficient slack is left in the fiber. A shift of position in the enclosure and strain causes the fiber to part. Fiber has a minimum bend radius. If this is exceeded a point of failure is set up. Micro bends can restrict light passage, attenuate the signal, and cause bits to drop or fail completely. The organization of the fiber may make it impossible to reach some fiber strands that are called out for splicing. This will make it necessary to performing the splice when the network is down for maintenance. This means paying crews on overtime scale to accomplish the work. Even if the fibers can be accessed, a poorly organized enclosure can require hours of time to unscramble and make the splice. Then hours more to organize and put back in place. These are hours that did not have to be spent if the job were done right the first time. As fiber counts in cables increase, the chance for failure also increases.
Enclosure integrity is very important to prolonging the life of fiber. Enclosures are designed to be watertight when assembled according to the manufacturer’s directions. However, if the technician is not careful and improper sealing occurs, water will infiltrate the enclosure. When this happens many points of failure can occur:
- Enclosure fasteners will corrode making it impossible to ever achieve a proper seal
- Bonding can be compromised making it impossible to locate the cable or worse, causing the locater to follow a different cable because water acted like a conductor and changed the bonding.
- Water can seep into a fiber tube, freeze, and put pressure on the fiber causing a failure outside of the splice enclosure
- Over time water can cause brittleness in fibers such that a repair in one area can precipitate repairs on other fibers.
- Splice enclosures in hand holes have been found frozen solid. Ice expanding inside the enclosure cracked the fibers, causing failure. In cold temperatures this can lead to an expensive repair since crews must first thaw the hand hole and enclosure before attempting a repair.
In a technically advanced industry, where critical infrastructure is dependent upon the reliability of fiber optic networks, why are some contractors not tuned into the quality of their technician’s work, and performing quality assurance checks on every splice enclosure?
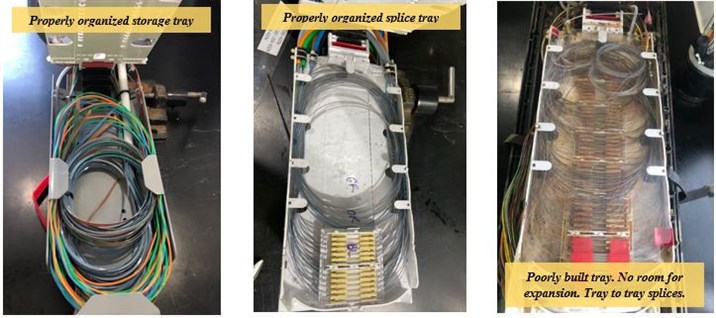
Standards for the construction of fiber enclosures vary by industry and customer. Fiber is a new area for many procurement organizations and the technical reasons for a properly built splice enclosure is a detail poorly understood by many decision makers.
Third party inspection is largely absent in the utility and telecommunication industries. As a result, contractors must set and maintain their own quality control programs. Construction companies that set high quality assurance and safety standards are the exception and can sometimes be underbid by others with lower standards. However, the true cost of ownership of a properly built splice enclosure versus one that is poorly built should be considered. Poor workmanship always adds to the total cost of ownership.
BUILDING A PROPER ENCLOSURE
What can be done to deliver a properly built fiber enclosure to the customer?
- Set high standards for enclosure construction and train employees to those standards.
- Build strong relationships with customers, communicate, and consult with them. Do not install an incompatible enclosure, even if the design calls for it, until the customer is informed of the potential problems it could cause
- Set up a mentoring program for new technicians to reinforce their training
- Do not force an installation. The customer may want another cable installed and be unaware that the enclosure cannot accommodate a new cable. Consult with the customer.
- Document all installations even if the customer does not require it. Include before and after photos, cut sheets detailing cable type, fiber count and a detailed list with the identity of each fiber spliced.
Given the critical nature of the infrastructure being controlled via optical networks, and the requirement for reliability, it seems that all companies should hold themselves to extremely high standards for splice enclosure construction. Splicing and splice enclosure construction directly affects network reliability. With the internet of things (IOT), critical infrastructure will depend on fiber networks performing flawlessly. Electric Conduit Construction will continue to do its best to exceed customer expectations and build quality and reliability into all of our work.